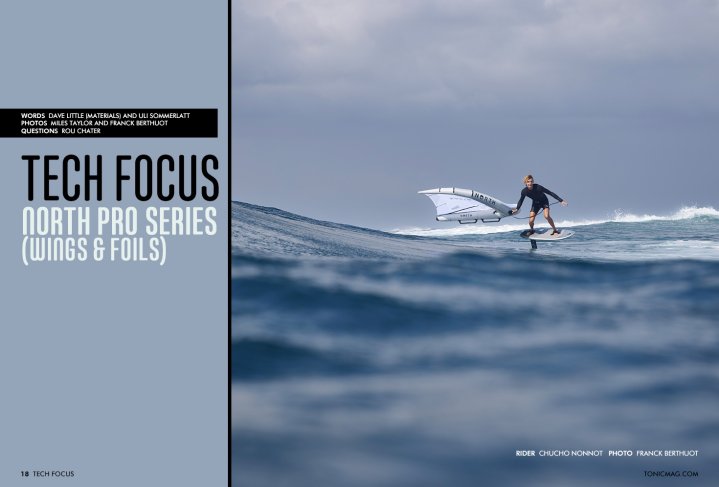
Tech Focus - North N-Weave45
Issue 18 / Tue 21st Nov, 2023
Dave Little and Uli Sommerlatt discuss North's latest Pro Series and the strides they have made in their materials. With a focus on refinement, North has been utilising bespoke options rather than pre-existing ones. One of their newest materials, N-Weave45, is lighter and stiffer than conventional Dacron, resulting in superior performance and efficiency in their wing designs. For those who like a little tech talk, this is for you!
Hi Dave and Uli, it's great to have you with us! We'd love to hear more about North's latest Pro Series. The materials have seen significant advancements lately and now form a major part of North's Pro Series lineup for 2024. How long have you been working on perfecting these materials to the point where they are ready for integration into the new products?
We never stop working on materials. When we're not producing new materials, you'll find us evolving the existing ones from season to season, as with the addition of the cross-ply laminate used to create N-Weave45. We constantly seek ways to refine our products to increase performance further.
North distinguishes itself by using its own bespoke materials instead of working with pre-existing options. Does this affect the speed of the process, and what are the benefits and drawbacks of manufacturing your own materials?
North Sails Advanced Textiles has been an excellent asset for the broader group. We can try many different options in material make-up reasonably quickly. Knowing our material will be our own and is purposefully developed for specific performance in a kite or wing and not just re-named mass supply product is a huge benefit. It's more complicated than buying a pre-existing material, but it brings unique performance and advantages to fine-tune the material properties as we require them.
Let's start with the N-Weave45, replacing the conventional Dacron on the wing structure. What makes it distinctive, and why is it better than the material you used before?
N-Weave45 is a high-tensile strength woven fibre reinforced with a Dyneema cross-ply laminate. We developed N-Weave45 to help reduce geometric compromise in the inflated structures. It is explicitly designed for wings – because it is stiff in all three directions. You don't need a wing to twist and turn like a kite, more the opposite. The inflated airframe needs to be torsionally stiff – much like the mast or rig of a sailboat.
Furthermore, you want the inflated airframe to be as stiff as possible in the high-loaded areas for maximum efficiency. Imagine you have an easy-to-bend airframe, and you start pumping it. You won’t get much efficiency out of a bendy wing - all you do is feather fabric through the air. Now, you do the same with a stiff airframe and a nicely tight canopy, and you get a great pull from the wing for every pump you engage the wings with.
N-Weave45 is still 30% lighter than conventional Dacron. The weight saving translates into more outstanding performance, more efficient power delivery in light air, and makes the wing more manageable in all conditions. This allows us to make smaller diameter LE and struts for our wing designs, reducing the drag of a wing and making it stiffer than a bigger Dacron LE wing, with significant weight savings.
It is 3x stiffer than Dacron in the warp direction. N-Weave45 is almost 4x torsionally stiffer than Dacron on the 45-degree bias when inflated to the recommended inflation pressure. From a manufacturing and performance perspective, the new 45-degree biaxial laminate layer stabilises the material, improving its consistency for greater integrity and durability of the airframe.
How is the durability of this new material, especially under harsh UV conditions, compared to other products on the market?
The UPE fibres used in N-Weave are well known for their resistance to moisture, most chemicals, UV and micro-organisms, and the laminates used by North Sails Advanced Textiles are proven over 1000s of sails made and used around the world in some of the harshest conditions.
We test every new material we make and trial. Then, we test production material lots.
Compared to other products on the market? I'm sure that most products are on top of UV nowadays. We still use standard Dacron and canopies in our wing range, which are long-lasting and durable.
High-modulus materials stretch little when pulled and have incredible resistance to deformation. This is important because if the inflated structure deforms under load.
UPE fibres also have extremely high cut and abrasion resistance. They are well known for their lightweight, their durability and their toughness. They are used in some of the most extreme conditions in things like military body armour, industrial-sized fishing equipment, and sails and ropes for racing yachts.
We hear lighter, stiffer, stronger all the time; why does that matter to the rider?
Without oversimplifying things, a lighter and stronger wing is more efficient, requiring little to no waste, effort or energy to achieve results. The lighter the wing, the more efficient the power delivery in light air and the easier it is to handle in all conditions. The stiffer and stronger it is, the more power it can generate and the greater the shape-hold, durability and longevity. A stiffer wing reduces structural deflection and transfers wind energy into greater forward speed while getting up on the foil or riding along, and explosive boost and hangtime for freestyle tricks.
When you combine these two attributes, you get a wing that can generate much more power for its size, that is lighter and, therefore, easier to handle.
A lighter and stiffer wing overall might also mean you could ride a slightly smaller wing size because it now has the same speed and power–generating performance as a larger wing.
Or you could look at it the other way and say that a larger wing, such as the Loft Pro, is lighter for its size, making it more efficient and easier to handle.
However, efficiency does not only depend on material choice. It also helps to consider all the design attributes of the wing, such as the LE size, Profile shape, Camber, Dihedral, Centre of Effort (COE) and TE Tension.
The new canopy material, Matrix HTRS, why did you need to create this, where is it used and to what advantage?
For a high-performance, high-speed wing, canopy tension and shape-hold are critical canopy attributes. Matrix is a low-stretch, high-tenacity, low-deflection canopy material explicitly designed to meet the demands of the new stiffer N-Weave45 airframe. It helps balance the tension of the rigid airframe, increasing the wind range and helping to hold the wing's shape in all conditions. Since the N-Weave45 airframe deflects less than a traditional Dacron airframe, an N-Weave45 airframe sees naturally higher loading. Therefore, it needs to be paired with a canopy material that can handle these higher loadings, which is what Matrix HTRS does.
How does it (Matrix) handle interactions with the foil? We understand this is arguably the primary concern for wing foilers' canopy tears; can we expect fewer issues with this new material?
Matrix is not just stretch-resistant... it's also strong, tough, and has remarkably high cut and abrasion resistance. However, carbon foils, especially when scratched on the tips, can be razor sharp for any canopy material.
You've also developed a new GripLock Carbon handle for the Pro Series. What's different about it compared to the standard handle on your other wings?
The Carbon handles are lighter and reduce the overall wing weight. Hence, they give the rider a faster, more direct, and more reactive response.
We all know that these new materials cost money to develop, but how does the Pro Series compare to other products using new materials? Are we talking eye-watering prices, or is it something more attainable for the weekend warrior?
Manufacturing materials in-house helps us to keep the costs down and then pass on those savings to our customers. Just look at the RRP of the North Pro Series on our website compared to wings made with Alluula or other materials, for example. The North wings are more affordable.
You still have the standard wing series, too, which is excellent; why should someone choose the Pro Series, and what sort of a rider is it for?
The Pro Series is for the discerning rider looking for an edge over the competition - or higher performance from their equipment. Although we don't market the Pro Series as entry-level, they are still incredibly accessible wings for all riders, and anyone - from the relative novice to the seasoned pro – will benefit from their performance attributes. The Nova is our all-round Freeride wing, with an effortless low-end and a massive wind range. It's easy to get up and ride without pumping your wing. The Mode Pro also has a huge wind range, but it might require more effort to get up and going than the Nova. The Loft Pro is a large wing to handle, but we recommend every rider has one in their quiver for those days when you need to get on the water and can't wait for wind.
Will we see these materials and technologies filter into new products as well?
We're already starting to see a crossover between various products in our foil/kite range – from small yet crucial details like the handle grips to introducing Pro materials into yet-to-be-released products (coming soon!)
Thanks, Uli and Dave, for taking the time to talk to us!
Thank you!
Videos
By Rou Chater
Rou Chater has been kitesurfing for over twenty years, paddleboarding for the last six years, and was there testing the first wingsurfer from Naish in Tarifa when it arrived on the continent. He is passionate about riding waves and exploring new places. As the publishing editor, he oversees everything at Tonic but also our sister magazines IKSURFMAG and IMB. He's been on the water since he was born and has never looked back, in the winter you'll find him chasing swells in the Caribbean and during the summer he can be found all over Europe at various SUP, Kitesurf and Mountain Bike events getting features for the magazines.