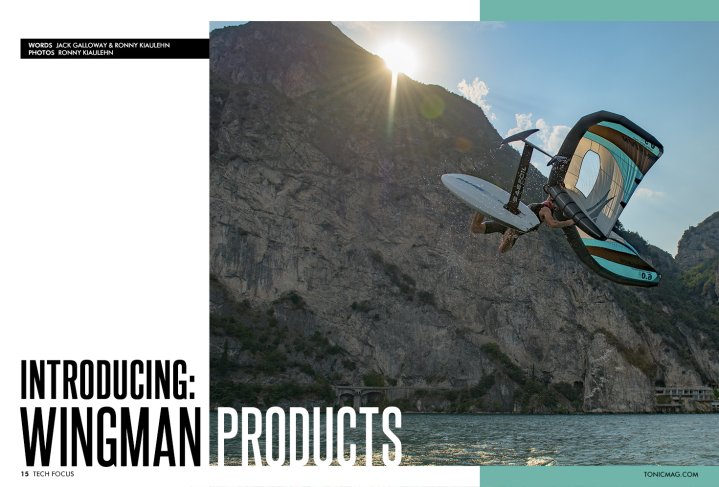
Introducing - Wingman Products
Issue 15 / Thu 23rd Feb, 2023
Learn all about Wingman Products, how they came to be and their state of the art impact vest & harness
Wingman Products are leading the charge in harness & impact vest design for wingfoiling. Their products are new & innovating, changing the way many of us perceive harnesses for good in the sport of winging. Jack Galloway chats to Ronny Kiaulehn to learn all about the brand, the products, and how it all came about.
Hi Ronny, Great to chat again! We did an article with you and your son Pietro a year & a half ago now on wing foiling in Lake Garda. It looks as though a lot has changed for both of you since then!
Hi Jack, yes when we did the last article we just started on our Wingman Products project. I remember Pietro using one of the first prototypes of our impact harness vest in the photos. Now Wingman Products is a small exclusive brand producing tailor-made high-end foiling accessories.
And now we also collaborate with ION on a few of their wingfoiling product designs.
I'm looking forward to hearing more. Could you start by introducing yourself & Pietro to our readers?
My background comes from windsurfing R&D. I was working as a test rider and accessory designer for Fanatic/A.R.T. in the early 90s. This is when I also started to work on harnesses. Back in 1992, we had a patented harness design called the “vertebra” concept. It had motocross protectors mounted on the back for protection and better power distribution. It was the first real hardshell harness design on the market. In 1996 I quit my professional windsurfing career and started working as a photographer which I still do today. For Wingman Products I only help out with the designs and producing photo/video content.
It’s my son Pietro that takes care of the production, prototyping, and most of the testing. He developed some impressive sewing skills and craftsmanship and he’s a pretty good wing foiler, too. The great thing about that is he can finish a prototype and gets it straight from the sewing machine on the water for testing. That saves us a lot of time and we can implement improvements very fast into our products.
So Pietro is the second generation of harness and accessory design and now, 30 years later, we got another patent for our Wingman impact harness vest design.
What gave you both the idea of creating Wingman Products and the impact vest & harness combo?
Pietro comes from BMX racing and freeride mountain biking. He was used to using protectors since he was a little kid. When he started wing foiling, the jumps got higher and higher. I was getting more and more worried about him getting hurt. All impact vests on the market only had soft foam protection. That’s ok as long as you are falling on the board or crashing on the water but does not help too much when you have an impact with the foil.
Then we had a look at Pietro’s bike protectors, they were all hardshell designs. So we thought that would also be a good idea for our impact vest.
The idea to make a modular impact harness vest came due to a heavy epicondylitis I had after a few months on Fuerteventura. I was not able to wing foil anymore. A harness was the only solution for me to get back on the water.
Making the harness detachable was the next step to adapt it to different riding styles: racing, cruising, long distance, and free riding with the harness module and if you go for a freestyle session you can just take the harness off and use it as a full hardshell impact vest.
Is it true that all your materials are from Europe? What was the reason behind that and how does that affect the quality of the finished product?
Yes, it is. We are trying to make our products with the best materials possible. Wingman is not producing any stock, we only take back orders. That allows us to improve our products continuously. Buying materials made in Europe means having short lead times and makes it easy for us to change materials or parts for better ones without any problems. Reordering materials is a matter of days. Ordering materials in Asia can take a month to arrive and maybe they would be already outdated for us the day we get them.
That's very unique in this market. Could you go into a bit of detail on where the various materials are from and where they are made? For example, neoprene, carbon, hardware, etc.
Our Neoprene is “Made In Berlin” from the only neoprene producer in Europe. They make single sheets of neoprene for us just the way we want them for testing before we order bigger quantities.
The carbon looking material we use for our protectors is not carbon. It’s a material called Curv. A self-reinforced thermoplastic composite that provides superior impact resistance. Basically indestructible. It’s also used for tactical and anti-ballistic gear. It’s the perfect material for our protectors and reinforcements. We also got a really cool Fidlock magnetic quick-release buckle on our spreader bar. Curv and Fidlock are both German brands.
This clearly has a positive impact when it comes to sustainability. Particularly when compared with brands importing materials or using labour from China etc. How important is this to you? Is there anything else you’re doing as a brand with sustainability in mind?
Yes, you are right. Wingman Products are 100% handcrafted in Italy. Most of the work is done in our tiny workshop at Lake Garda and we get some help from a sewing factory at Lake Como - A small family-owned business. They specialise in custom-made diving suits and are able to produce small quantities of very high quality. But the most important for us is their flexibility to quickly change and improve things from one batch to the other. The short transportation route gives us the possibility to better control the quality of our products. I think building long-lasting products is one of the most important steps toward sustainability. Producing in this tailor-made style results in much higher production costs.
Am I right in saying the harness hook is 3D printed? How did that come about? There must have been a lot of R&D in getting the design just right.
Yes. It’s incredible how strong high-quality 3D prints are right now and also how nice they look. We found a company on the Adriatic coast that prints all our plastic parts. Apart from the hook also parts of our Loop, the mono harness line, are 3D printed. We are still making big steps to improve our designs every day and we are working on new ones all the time. 3D printing lets us fine-tune our designs to perfection. But there is also a dark side to it. 3D prints are very, very expensive compared to injection moulding. To give you an idea: The price we pay for a 3D-printed hook is probably 20-30 times higher than a moulded one. Investing in a mould now would be too early for us as we are still developing. But that would be the next step. Let’s see what the future brings.
Your harness hook is higher on the chest than you’d find on traditional kite & windsurf harnesses. What is the reason behind that? How do you stop it from restricting your breathing?
Yes, we are convinced the high hook position is the way to go. There are only advantages from our point of view. First of all the wing is in its natural position. Compared to a waist harness you can use a shorter harness line which results in less swinging and it’s really easy to hook in and out. When you are hooked in the harness line is about 90° to your chest, so it’s not pulling the harness up or down. The high hook position also allows you to de-power your wing above your head without unhooking. When you start climbing on the board the hook is already above the rail so it won’t damage it.
Also paddling lying on the board is easy. You can place the hook between your front straps to keep you in a comfortable position. Riding in switch hooked in is also possible because your chest turns around much more than your waist.
Yes, you are right, a chest harness can restrict your breathing if you tighten them enough so the hooks stays in a stable position, and if you leave it loose enough to freely breathe the whole harness and hook will move all over the place. Resolving that problem was one of the biggest challenges of the whole project. The solution was to design the harness module in a way so it can breathe with you. We found a way, the circumference of the harness can extend by about 8cm which is enough to breathe freely and at the same time our pre-tensioned velcro system fixes the hook firmly in position. We call it the breathing harness system.
Lake Garda must be the perfect spot for testing gear. Does Pietro do most of your testing or does your growing list of pro riders feedback on their opinions too?
Pietro does a lot of testing together with Alesandro Tomasi who lives also at Lake Garda. Balz Müller passes by a few times a year and gives us very important input. But we also get feedback from many other athletes using our products. We are really proud to already have many pro riders using our gear: Francesco Cappuzzo, the Zorzi brothers, Gollito Estredo, Luca Franchi, Nicolò Spanu, Giulio Gasperini and the list is still growing. Having those riders testing our stuff in all kinds of conditions around the world helps us a lot to improve our products all the time also in terms of durability.
We can’t wait to test the Wingman but I have to ask; what else can we expect to see from Wingman Products in the future?
We will be super happy to set you up with everything you need to get you “hooked” on our impact harness concept. At the moment we are working on a light harness version and a modular impact vest. We are currently in Fuerteventura setting up a small workshop for prototyping. Of course, we will share the news as soon as the new products are ready.
By Jack Galloway